2020 has been a year like no other. AMT worked hard to keep its members informed with the most important information and news in the industry and launched a news blog and weekly e-newsletter to make the information timely and actionable. As the year comes to a close, we ask ourselves what the key takeaways of 2020 will be for the manufacturing industry as a whole. The industry experienced a great deal of volatility, but what changed in the long run? What trends, if any, accelerated or decelerated?
There are still many unanswered questions, and it may be too early to predict the fallout; however, we think it is realistic to make a few projections.
Ending or minimally slowing a decades-long outsourcing trend, the manufacturing supply chain is being critically reevaluated and parts of it are likely to be reshored in the next several years and automation will be part of the reshoring solution.
Additive manufacturing (AM) was thrust into the spotlight and demonstrated its value in new ways, accelerating its use cases.
Lastly, new, technology-enabled business models proved to be critical in manufacturing sourcing.
Reshoring and automation
The pandemic exposed critical vulnerabilities in manufacturing supply chains in the United States. There has been talk in all corners of the industry and on Capitol Hill about the need to reevaluate U.S. dependence on offshore suppliers and the need to reshore critical supplies going forward.
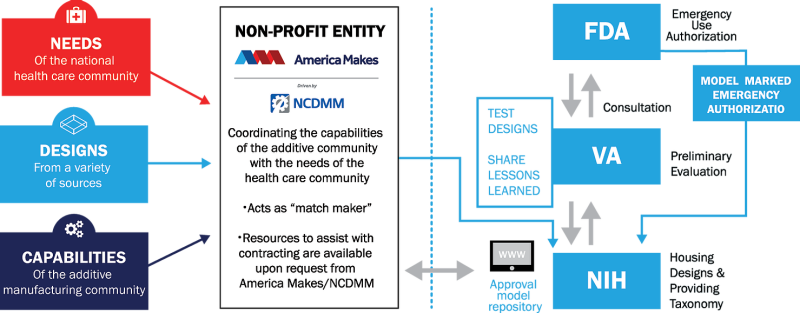
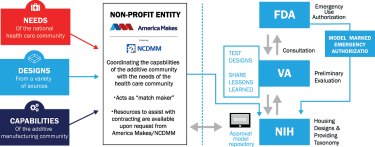
“It is not yet clear how significantly the pandemic will change North American supply chains as most companies are still in the planning stages,” said Pat Walsh, vice president, Ehrhardt Automation Systems. “The $100,000 question is whether there will be sustainable changes in supply chains or if this will all be forgotten six months after there’s a vaccine. Reshoring will require significant capital investment, strategic planning, and hiring new types of employees with different skill sets. These are long-term decisions, and they cannot be made overnight.”
Walsh, like many others, believes that manufacturers’ reevaluation of their supply chains and companies’ reshoring initiatives will lead to a dramatic increase in the demand for North American (NA) components and equipment. If there is even a 10% increase in the demand (and it is likely to be much more) for more NA products and parts, automation will be the only solution to meet this growth. There is not enough low-skilled labor in the United States to make reshoring affordable without automation. The challenge of finding enough workers, coupled with the variable cost of labor, are real limits on growth. Automation, on the other hand, can scale indefinitely, and it is a capital cost that can be depreciated over the life of the equipment.
Walsh thinks that reshoring, if it truly takes root, will likely be driven by the demands of the largest manufacturers, such as the big three automotive companies and the transplants from Japan and Korea. “They experienced significant delays due to the pandemic, and they will want to protect themselves from potential future disruptions. If they mandate that more of their products be sourced from NA components, it will drive the rest of the market,” said Walsh. Automakers will keep a lid on costs, which will drive automation in their supply chain.
Fighting COVID-19 with 3D printing
Additive manufacturing (AM) proved itself as a very real-time solution in a very serious crisis. It enabled rapid prototyping and iteration(s) of PPE components and supplies – face shields, testing devices, masks, parts for ventilators, temperature-measuring devices and more – and decentralized PPE production to meet regional and local needs. There is no aggregate national data on the total quantity of PPE and components produced through AM, but it is clear that it played a role in providing regional and national supplies.
“AM was a game changer not in terms of the quantities a single manufacturer could produce, but in terms of what the entire industry collectively did. Two of the most effective things the AM industry did was widely share prototype designs and enable production to meet specific regional needs as they arose,” said Andrew Resnick, director of communications and public affairs, America Makes.
America Makes, the nation’s leading public-private partnership on AM technology and education, joined forces with the Food and Drug Administration (FDA), the National Institutes of Health (NIH), and the Veterans Health Administration (VA) to develop an online portal to connect health care providers in need of medical PPE with manufacturers with 3D printing capabilities and designers willing to share 3D print designs. NIH reviewed and vetted the submitted designs.
To date, the online portal has collected 685 total submissions from over 400 manufacturers. The FDA reviewed submitted designs for clinical use or community use. To date, there are 617 designs; of which 514 are prototype designs; 34 that have been reviewed by the FDA for clinical use and 28 that have been reviewed for community use. These can be found on the NIH 3D Print Exchange site (https://3dprint.nih.gov/collections/covid-19-response).
America Makes is now working with NIST and the Office of the Secretary of Defense on planning a second phase in which they will develop a response framework for possible future crises based on lessons from the pandemic.
On-demand manufacturing marketplace accelerates
In the private sector, Xometry’s innovative business model, and the largest on-demand manufacturing marketplace in the United States, connected requests for PPE supplies with available manufacturing capacity nationwide. With more than 5,000 manufacturing partners in their network, the company was uniquely positioned to facilitate the production of face shields, masks, visors, biospray sanitation equipment, temperature measurement devices, ventilator parts, and more.
“With more than 12 manufacturing technologies, including 3D printing, Xometry really stepped up not just to connect buyers and capacity in manufacturing parts, but as a supply chain and logistics partner. People came to us and said, ‘I’m looking for an ISO 1345 shop with die cutting to make face shields,’ and we were able to very rapidly find these specific fits in this time of national chaos,” said Greg Paulsen, director of application engineering, Xometry.
“We’re still selling a transparent, full-face protective shield developed through open source design and made completely of PET material. We found an ISO-13485-certified medical device manufacturing facility on our partner network who could make 10,000 a day. It was a mass-production stopgap solution (an FDA Emergency Use Act directive allowed production of PPE stopgap solutions without having to go through the formal FDA approval process) and enabled the manufacturer to bring some staff out of furlough as well. We then turned it into an e-commerce item to make it more accessible nationally and directed people where to go buy the shields,” said Paulsen.
In our 2019 white paper series on transformative technologies, AMT discusses both additive manufacturing and new business models in manufacturing. For an in-depth exploration of the challenges and opportunities of reshoring the U.S. supply chain, refer to our latest series of white papers. To access these white papers, go to www.AMTnews.org/white-papers.