The skilled labor shortage has made it abundantly clear that manufacturers need to change how they recruit new hires. Humanmade, a non-profit in San Francisco, is setting a new model for workforce development by bridging the gap between the unemployed and underemployed to the career pathways and financial security of manufacturing industry careers.
Humanmade was started in 2018 as part makerspace, part advanced manufacturing training center, and part youth career program. The mission was not only to fill a void from TechShop, a makerspace franchise that went bankrupt in 2017, but to expand the maker space model into an equitable and inclusive training opportunity for all. The organization goes beyond just skills development and helps reduce social barriers that can hinder people from fully achieving their career potential.
“We distinguish Humanmade from traditional makerspace or workforce development models to create a diverse and equitable manufacturing ecosystem,” says Ryan Spurlock, founder and executive director for Humanmade. “We provide new career opportunities and eliminate the traditional barriers that people face when trying to gain entry into the advanced manufacturing sector, such as financial resources or a formal college education.”
Reaching beyond the traditional
Humanmade’s program is reaching a wide age range (18 to 70) and a large percentage of underrepresented populations: 90% are below median income, 70% are people of color, up to 50% are women, and 7% are in the LGBTQ community.
A surprising 50% of the graduates were unhoused or experiencing housing instability prior to coming to the program, but now they have the resources to get an apartment and provide for their families. The one thing they all have in common is that they are looking for an opportunity to enter a career that requires less than a four-year degree and has many of the same outcomes as one as well.
There’s a great opportunity for manufacturers to find new hires in non-traditional populations by contacting community-based organizations that have training or apprenticeship programs.This approach is a win for everyone involved: the individual, the company that ultimately hires them, their families, the communities they call home, and society as a whole.
Free training for all
Humanmade is funded by grants and corporate sponsors, as well as membership fees for the makerspace. That money is used to subsidize the Next Generation Manufacturing Skills Program, which is free to participants. The program includes 12 weeks of hands-on, project-based training in 3D printing or CNC machining, including learning to read blueprints, use CAD/CAM software, and operate machinery. There are morning and evening classes available to meet different schedules, with four instructors and three primary shop areas full of advanced technology manufacturing software and equipment.
A rapid prototyping area includes 3D printers, lasers, a textiles department, and a computer station with all necessary design software. The metal shop, where the CNC program is held, houses all metal working tools including two Tormach CNC mills and a complete welding station with Fronius multi-process welders. The woodshop includes all essential woodworking tools as well as a wood lathe and two ShopBots.
After completing the program, graduates receive assistance with job placement at local manufacturing companies or enrollment in additional skills training. Participants gain the foundational knowledge needed to enter jobs such as CNC operator, assembler, technician, and machine maintenance. Humanmade has partnered with AMT member Autodesk to offer program graduates a free opportunity to take the Autodesk industry-recognized certifications.
Over the last two years, 89 participants have gone on to manufacturing jobs, but support doesn’t stop there. Humanmade also checks in with grads for up to a year after they leave the program. During that time, they are given free access to the makerspace, free classes and ongoing training, and regular meetings with a case manager.
“We want folks to be successful post-placement,” Spurlock explains. “A lot of organizations put someone in a job and dust their hands off because they've done their part. We believe it's not just a placement, but it's also helping someone be successful and making sure that they can maintain that new opportunity.”
Through his previous experience at TechShop, Spurlock saw that people who were most limited by financial constraints (those with the biggest opportunity to benefit) were being turned away from the traditional makerspace model. He used that idea, along with insight from the manufacturing community, to bridge the gap between the needs of the sector and the underserved communities that need jobs and opportunities.
Spurlock has seen people come into the program with little to no knowledge of making or manufacturing. They leave with the basic knowledge to be successful and for an employer to take them on and help them grow into where they need them to be. These become transformative experiences where they’ve gained life-changing skills to build on their future.
Reducing all barriers
Humanmade goes beyond teaching hard skills and helps participants navigate the challenges that they faced prior to entering their program and navigate some of the barriers they face, such as housing, childcare, financial resources, and food insecurity. Participants engage in regular support meetings and case management assessments to determine wellness needs and available resources.
Since COVID, the number of people looking for help has increased. Humanmade partners with other organizations to provide free meals to food-insecure program participants and to facilitate resource and service referrals for other basic needs.
“We can provide the resources and as much barrier mitigation as possible, but if the existing societal and economic pressures continue to increase, it's harder for people to complete the program,” Spurlock says. “We've really had to double down on our soft skills to make sure that folks have the ability to successfully complete our program.”
Despite the economic pressure and resource shortages the students are experiencing, Humanmade’s support services have enabled a substantial number of students to complete the program and secure meaningful employment in manufacturing.
For more information, visit Humanmade.org.
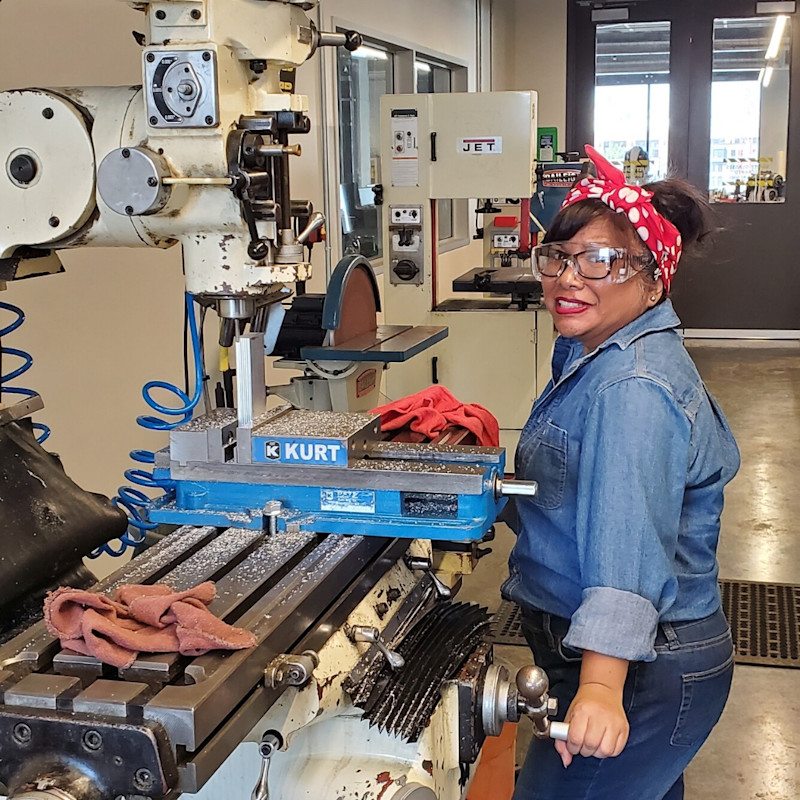
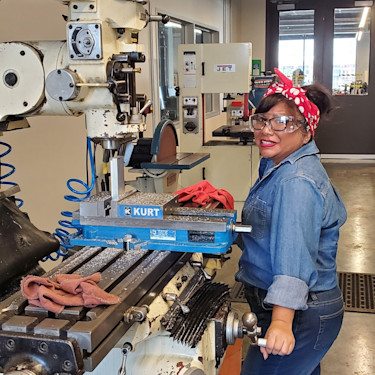
Maria Llorente-Quan is not only a Humnamade CNC Milling Program graduate, but she is now one of Humanmade's instructors that supports current participants in mastering the foundational skills needed to attain a life-changing entry level career in the Advanced Manufacturing Sector.
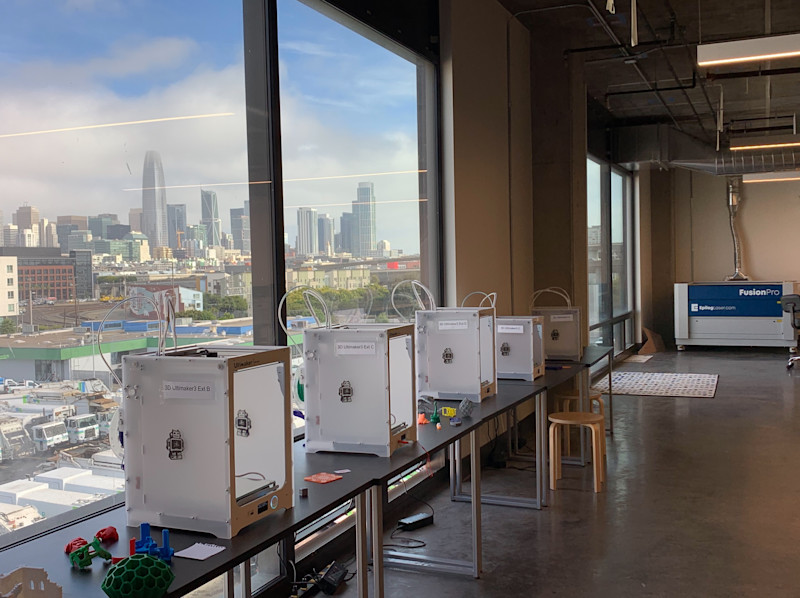
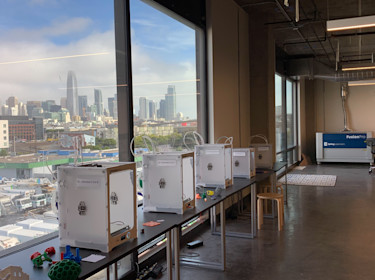
A few of Humanmade's Ultimaker 3D printers that both members and workforce participants utilize while overlooking the San Francisco skyline.