In part one of this series, I discussed the importance of a strong U.S. apprenticeship program and how its success would sustain manufacturing jobs at home, while helping to reshore millions of manufacturing jobs. In part two of this collection, you meet five more successful manufacturing leaders who started their careers as apprentices – proving a university degree is not an indispensable criterion or, at least, not the required first step to achieving career success.
Winning with alternative routes
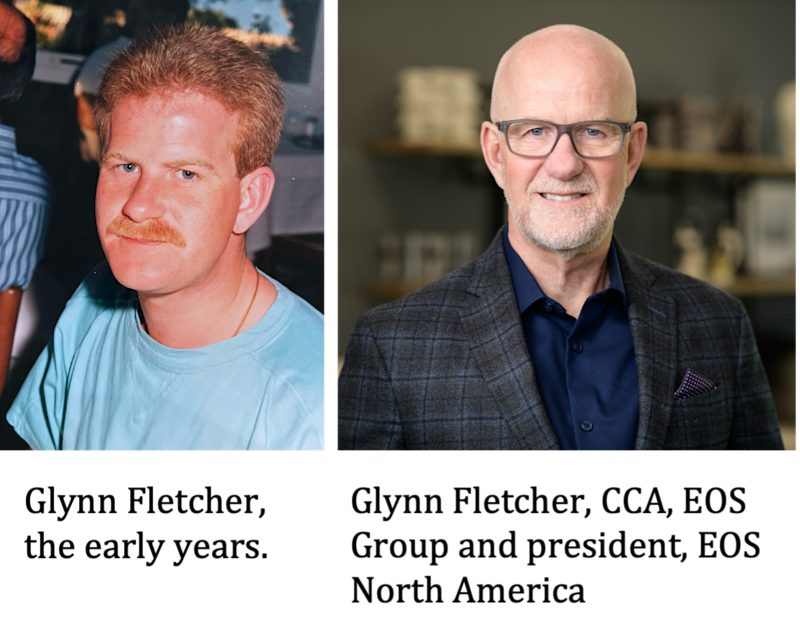
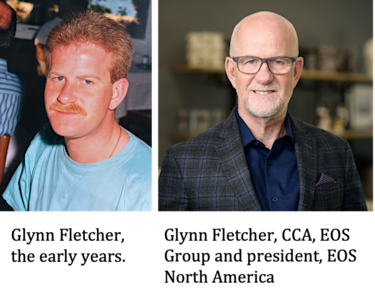
Glynn Fletcher is chief customer advocate of EOS Group and president of EOS North America, (IMTS booth #432302)a global leader in high-end solutions in industrial 3D-printing. Fletcher holds a senior executive position at the EOS worldwide level and leads the company’s operations in North America. Fletcher joined EOS in 2015, bringing with him more than 30 years of experience in the CNC machine tool industry. Fletcher started his career as an engineering apprentice at the then U.K. truck manufacturer, Fodens Limited. After gaining his credentials, he worked as an international service engineer, undertaking assignments in the Middle East and Africa. Fletcher has also pursued continuous learning throughout his noteworthy career and has even lectured at Yale University.
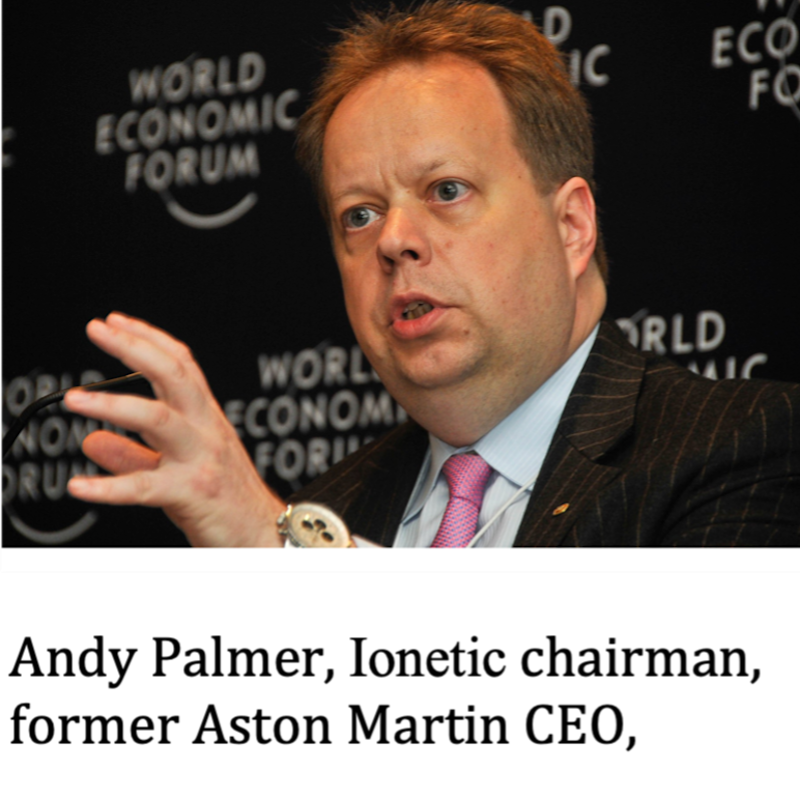
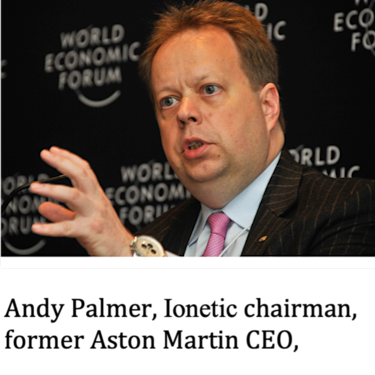
Andy Palmer, chairman of Ionetic, began his career as a technical apprentice for an automotive products company. After leaving school at age 16 and uninterested in attending a four-year university, he began an apprenticeship –which seemed to him like an excellent alternative. Palmer’s recipe for achieving career success included continued learning to gain qualifications, and deep industry knowledge. Palmer became a director at Nissan and later, the CEO for Aston Martin.
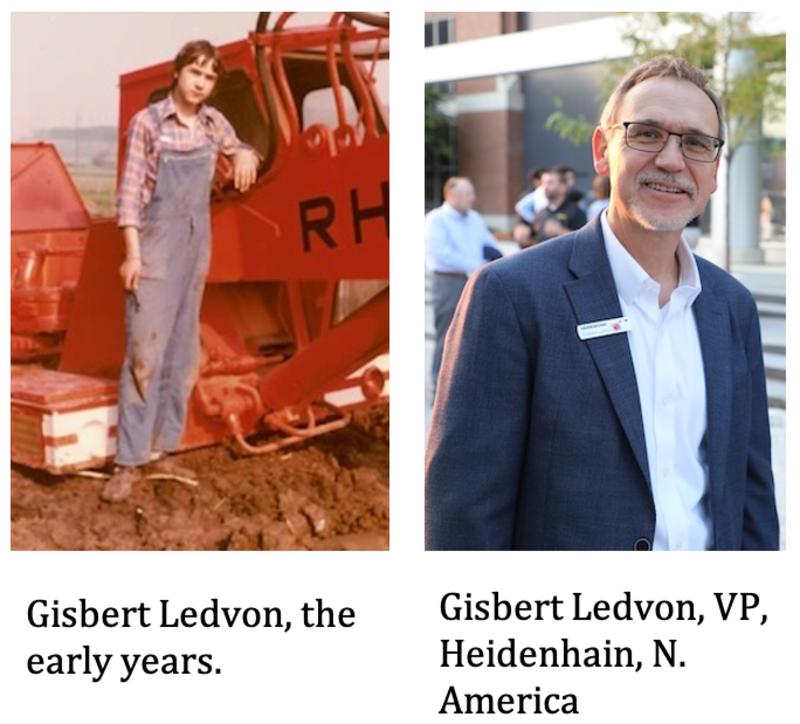
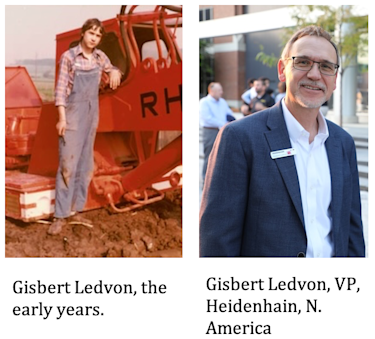
Gisbert Ledvon is vice president of marketing at Heidenhain North America, an industrial equipment supplier located in Schaumburg, Illinois, (IMTS booth #339440). Ledvon has spent the last 35 years with international machine tool, controls, and motion control companies. Born in Germany, Ledvon began his professional training as an apprentice via the Tool and Die Vocational College in Olsberg, Germany. Ledvon has lived in the U.S. for 30 years now, and has continued learning throughout his impressive career, including completing a program at Northwestern University’s Kellogg School of Management.
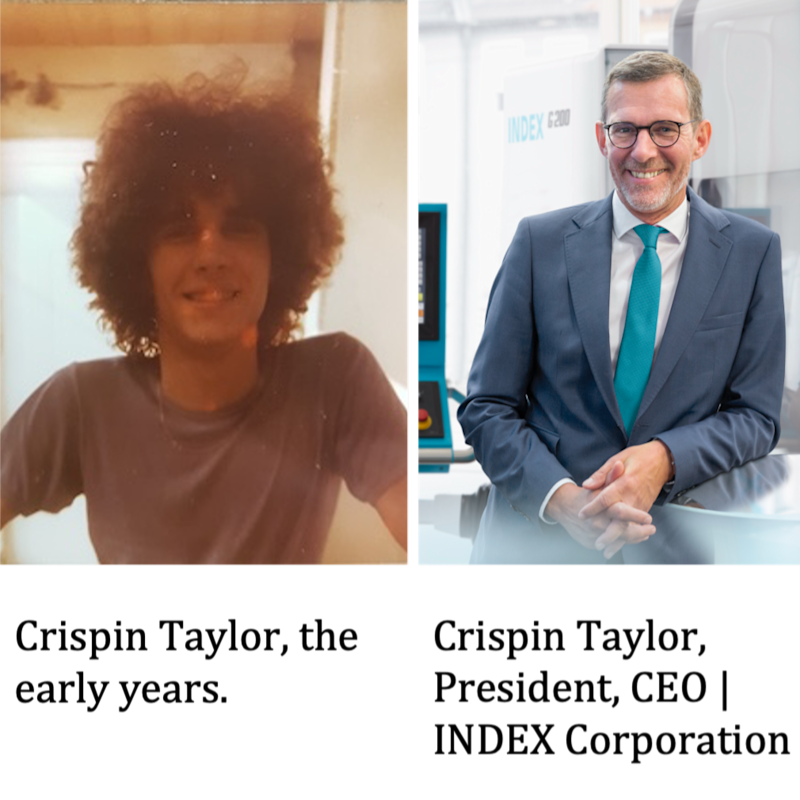
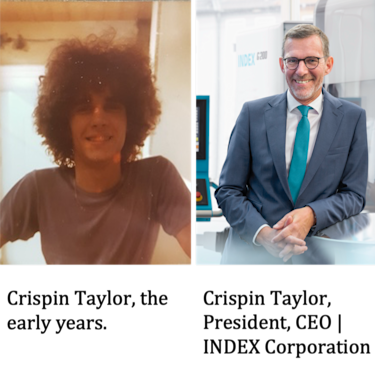
Crispin Taylor, president and CEO of INDEX Corporation, (IMTS booth #339119) in Noblesville, Indiana, a leading manufacturer of CNC turning machines, began his impressive career with an apprenticeship as a machine tool engineer and then later became a Master Craftsman. Taylor’s deep industry knowledge includes 30 years of experience in the machine tool industry, both in the EU and the U.S. Taylor comments, “Otherwise, I’ve never seen the inside of a college or university.”
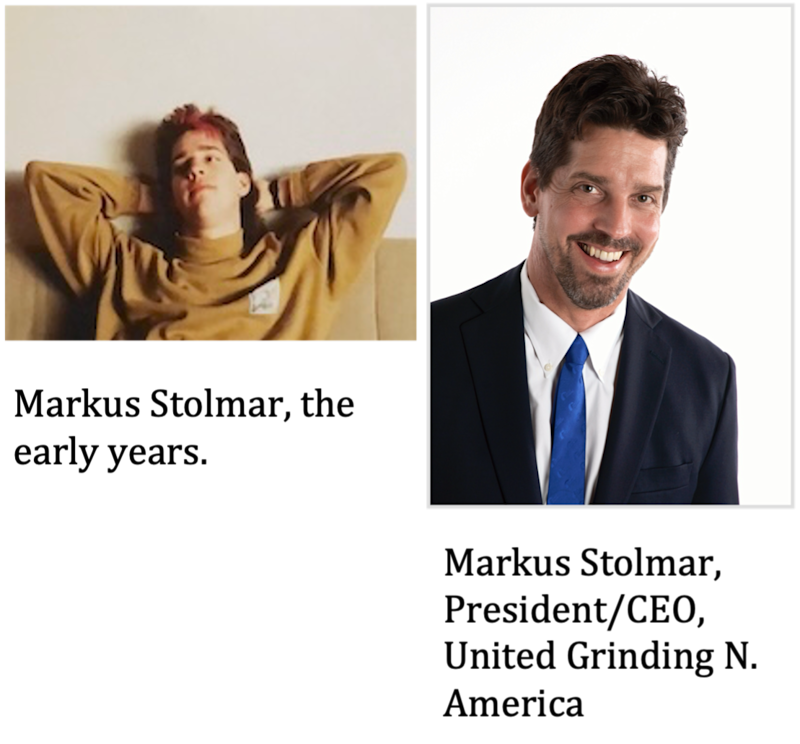
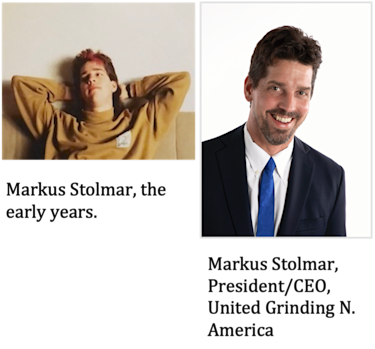
Markus Stolmar is the president and CEO at United Grinding North America, Inc. (IMTS booth #236802) in Miamisburg, Ohio. Prior to his undergraduate degree, Stolmar completed a three-year apprenticeship as draftsman. He went on to graduate from the University of Applied Sciences Würzburg, Schweinfurt and Aschaffenburg in Germany, earning a diploma in business and engineering. He then completed an executive MBA with Georgetown University’s McDonough School of Business. “We have a huge, collective responsibility to educate, inform, and engage the next generation of workers in our industry,” says Stolmar.
Follow the leaders
Leaders, trailblazers, innovators — they motivate, guide and manage individuals, and shape companies. Apprenticeships can jump start a career, create quantities of competent trainees, and prepare our future leaders with deep industry knowledge.
“Tell me and I forget, teach me and I may remember, involve me and I learn,” — Benjamin Franklin.
Share An Apprentice-to-Leadership Story
Did you begin your career with an apprenticeship or know someone who did? Share their stories with us to promote manufacturing apprenticeships nationwide and to recognize industry leaders. Please contact me at harry.moser@reshorenow.org.
Are you thinking about reshoring?
Let’s collaborate to support skilled workforce development and rebuild the U.S. manufacturing base. For help, contact me at 847-867-1144 or email me at harry.moser@reshorenow.org. Our main mission is to get companies to do the math correctly using our free online Total Cost of Ownership Estimator® (TCO). By using TCO, companies can better evaluate sourcing, identify alternatives and even make a case when selling against offshore competitors.