In an old, renovated duct factory in Ravenswood (a mile northwest of Wrigley Field) in Chicago, a small distillery is putting high-tech monitoring technology to good use in the service of something decidedly unglamorous: consistency.
No, not consistency in terms of texture or viscosity or even “mouth feel.” In this case we mean consistency as in reliability – as in making the same product over and over again without any changes in quality, appearance, or taste. It’s something we take for granted every day, assuming that the product we’re buying will behave the same way it did when we bought it last month. But it isn’t something that happens on its own – manufacturers take every step they can to ensure quality, reliability, and consistency, and they use a lot of high-tech equipment to do it.
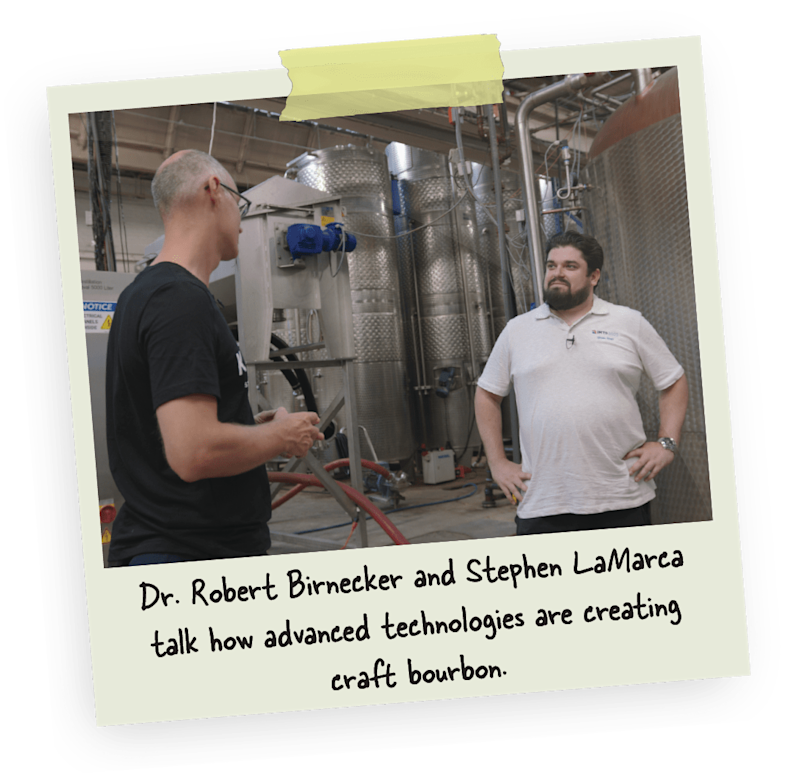
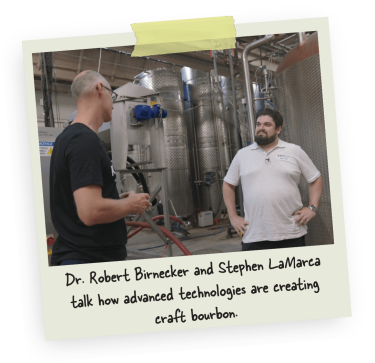
Leveling the Playing Field
For a process with as many variables as distilling, consistency can present a challenge to smaller, less tech-oriented craft companies. But that’s not KOVAL. For husband-and-wife founders and operators Dr. Robert Birnecker and Dr. Sonat Birnecker Hart (first name pronounced like a Shakespearean “sonnet”), distilling with advanced monitoring technology is a crucial part of their process.
“We’re not working on the same scale as a large distillery, but that doesn’t mean we want to have any less tech to make sure our process is fully monitored the whole way through,” Birnecker Hart says.
For KOVAL, what this looks like is a classic example of Industry 4.0, wherein every piece of equipment has a monitor on it and is communicating with a central system. “We’re able to keep tabs on all of the elements related to the distilling process,” Birnecker Hart says. “From what’s going on inside the equipment to what’s going on outside – the ambient temperature, the flow rate inside, the temperatures inside the mash tanks. All of these things are really important for maintaining consistency across the product.”
It’s All in the Details
Smaller distilleries that don’t use this technology, or that don’t have sensors on their equipment, will typically experience more aberrations and variation in their final products. Moreover, they might not know if something goes wrong until the whiskey hits their lips.
KOVAL doesn’t have this problem. “Every piece of equipment is fully monitored, so if something is off one point on temperature, we get an alert sent to us,” Birnecker Hart says. “We know in real time and can make changes accordingly.” This tech-forward monitoring approach means a more reliable manufacturing process and a more consistent product, as well as a lot less waste, since errors and issues can be addressed right away and not before they’ve already pickled a whole batch.
There are myriad other ways that KOVAL’s distilling process and final products are distinct from other operations – they use all-organic, locally grown grains, rely on only the prized “heart cut” of the distillate to make their products, and make rye, oat, millet, and other grain whiskeys with mash bills made from 100% of the named grain (most companies use a blend of grains at different ratios; rye whiskey, by law, only has to have a mash bill that’s 51% rye).
But none of it would be possible without the company’s novel deployment of advanced monitoring technology and automation. All of the data KOVAL collects goes to good use ensuring that their products taste the same today as they will next month, next year, and beyond.
Watch host Stephen LaMarca talk big data and bourbon on the special edition of “Road Trippin’ with Steve” at KOVAL on IMTS+, IMTS.com/RTWSkoval.
For questions about IMTS+, Michelle Edmonson can be contacted at medmonson@AMTonline.org.